Big. In theory, at least.
First of all, the rocket isn’t re-usable, so every bit of cost you can remove from the structure is cost you save ON EVERY LAUNCH. And the cost savings can be big. Just using some nominal numbers on the back of this envelope here, and I guesstimate a delta-vee savings of 500 m/s (it takes a vehicle around 10,000 m/s to get to low Earth orbit, starting from the surface of the Earth) would result in about a 21% decrease in overall vehicle weight, for the same payload. If you squint hard enough, the cost of an aerospace vehicle is almost linearly related to weight, so that’s about a 21% cost savings. Not bad, especially when rockets that go to LEO are about $50 - $100 million smackaroons each.
This reusable launch platform isn’t going to be cheap, but you only have buy it ONCE (unless @BeachAV8R is flying, then you’d better get a backup) . Say this Roc thingy costs $100,000,000 to buy, and you can save $20,000,000 on each rocket you build to launch from this higher altitude. The thing pays for itself in a mere 5 launches!
Wow!, right? Sign me up for two!
But, unfortunately, this is where reality comes crashing in to ruin all your dreams. Again.
I have no idea what the actual math looks like for this project, but I’d expect a hefty development/build cost on this plane, and “return on investment” is probably going happen around more like 100 launches. Whatever the actual number is, the launching aircraft is going to have to be in service a long time before it breaks even. And during that service, it’s going to wrack up life-cycle cost.
Life-cycle costs are simply astounding. Think of all the gas you’ve put into your car; and oil changes, tires, windshield wipers, tolls, parking fees, repair costs, inspections, insurance, registration, etc. And your car isn’t a high-tech airplane that carries rockets to the stratosphere. Maintenance/upkeep, training, inspections, re-certifications, accidents, etc. will stack up steeply from Day 1 and subtract from the bottom line. These costs nearly always far exceed the initial purchase price (or “first cost”) and more than a few careless investors have never realized a return on investment due to this life-cycle cost creep.
Another challenge will be finding payloads - rockets will have to be specifically made to launch in this style (Orbital’s Pegasus is one example in a pretty sparse field of air-launched orbital delivery trucks) and, as we established above in my airy conjecture, this platform will need a plethora of launches to make its return on investment. Aerospace developers can’t exactly be excited about dumping their money into designing a vehicle for a very unique and relatively high risk launch platform - if the Roc fails, how else do they launch their rockets?
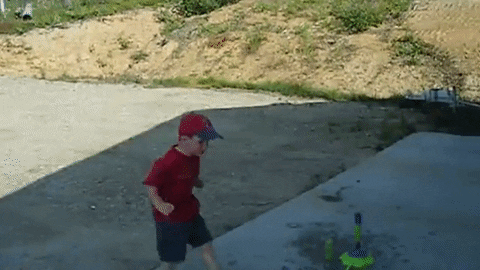
You don’t get into rocket science without being a rocket scientist, so I’m certain Señor Allen and his band of crafty aerospatial engineer Vuclans have thought through all of this (and a whole bunch more). I fully expect that they’ve worked out a solution that will turn a buck…but it’s not going to be easy money.
Good luck to them!.